If you have the need to use cooling towers in your business, you know exactly how important they are to the whole operation. Things that heat up during operational processes need to be efficiently cooled down so that everything keeps running smoothly, securely, and optimally. Therefore, without fully operational cooling towers in place as well as the proper maintenance, things will start slowing down and the whole business will suffer. To prevent this, you have to know and understand why it is so important for your cooling tower system to always remain fully operational. In this article, you will learn exactly that.
An Overview
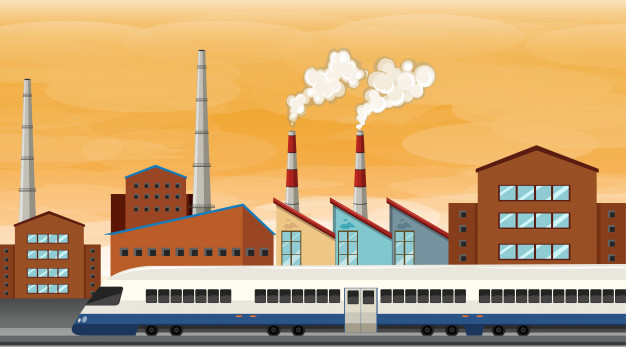
Chances are that you already know what these are if you have found your way to this article. Be that as it may, there is a lot more to understand regarding these facilities that you need to know if you are to maximize their cooling potential. For example, knowing a bit more about their history and features cannot hurt as there is always something new and exciting to find out.
A cooling tower is essentially a heat rejection device that deals with waste heat by cooling water. The stream of water is cooled to low temperatures and the towers either use evaporation to remove the heat out of the fluid, or air. Evaporation cools it down to wet-bulb air temperature, while the air cools it just near the dry-bulb temperature.
These types of cooling towers are mostly used in plants and refineries where there is a lot of heat buildup. Some of the places that use them most often and most efficiently include petrochemical and chemical plants, oil refineries, thermal and nuclear power stations, as well as HVAC systems that cool down buildings. The air induction into the tower is what classifies the different types. There exist induced draft models and natural draft models.
Regarding their size, they vary from small to very large. The biggest circular ones can measure up to 200 meters in height, and 100 meters in diameter. When it comes to rectangular versions, the biggest ones reach more than 80 by 40 meters. These structures are quite dominant in the general landscape of a factory or a plant and inexperienced people often mistake them for chimneys.
The towers first started appearing as early as the 19th century when steam engines with condensers were dominant. The modern hyperboloid tower is the patent by two Dutch engineers, Gerard Kuypers and Frederik van Iterson, who helped the first structure to be erect in 1918 near Heerlen. England became the dominant country to use in the first part of the 20th century, with the first ones being built around the country from 1924 onwards.
Nowadays, there are four different heat transfer methods. They include closed circuit, wet cooling, dry cooling, and hybrid cooling. All of them are common and used in specific cases, depending on the needs and regulations involved.
Cost Saving
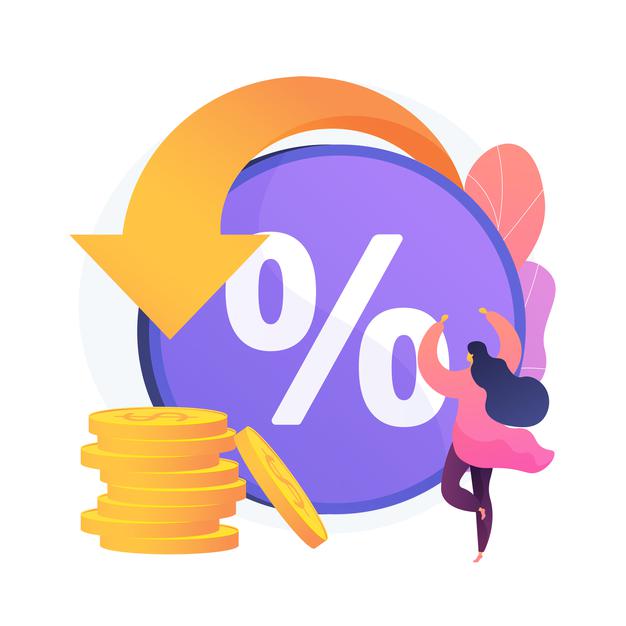
Now that we have reached the section of why it is so important to maintain operation levels of the cooling towers, we have to mention the most obvious thing first. That is of course the saving of unnecessary costs. If you keep everything running smoothly, you will increase the life expectancy of the whole system. This in turn helps with less need for repairs and changing of parts. The performance will be better, not halting production and operation and therefore allowing for a continuous stream of revenue.
Cooling Tower Repair Upgrades
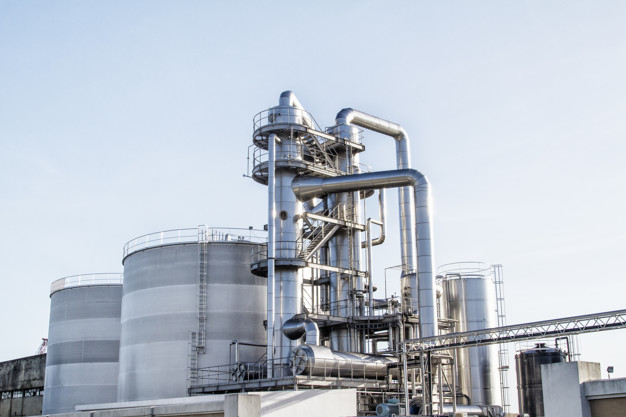
Modern technologies and innovative practices have become increasingly available for wider use and they can truly take your cooling tower efficiency to the next level. If you want them to be fully operational and stay that way for years, make sure to check out some of these new features. For example, Industrial Cooling Solutions has everything you need and more so be sure to head to their website and browse for a while. They offer repair services like counterflow, low drift, forced draft, and much more. Regarding the upgrades, decking, thermal upgrades, fan deck and structural replacement, and other major and minor upgrade services are all available.
Maintenance Tips
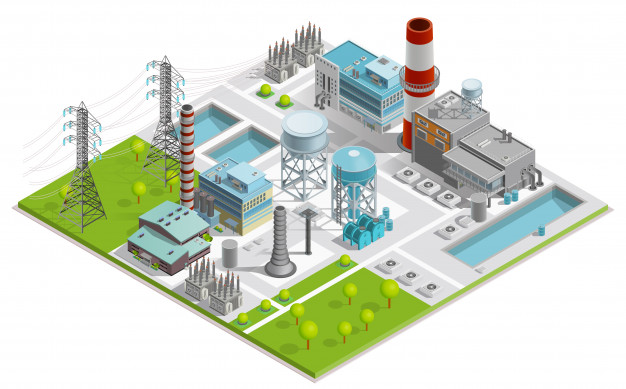
We will start things off with 10 crucial tips regarding the maintenance of your towers. You should definitely go out of your way and try implementing most of these, that is if you want to be at optimum capacity at all times
- Frequently check for the general condition of each unit and pay attention to strange sounds and noises. Many issues can be identified if things do not sound right.
- Lock-our procedures should be in full effect before hands-on work and all the motor switches must be disconnected for maximum safety.
- Make sure to inspect water distribution systems and check for dry areas to prevent buildup of scale. This will increase system capacity. Also, check for cracks and/or clogs on the nozzles.
- Clean any debris from, in, or around the strainers. Excess materials have no place in the system.
- The cold water basin should not have debris and dirt inside, so flush it through the drain or strainer. Water filtration has to be maintained. A good thing to have is basin sweeper piping as it functions as a form of automatic maintenance.
- A predetermined water level at the makeup water supply is important. It helps with water conservation and lower entrainment of air.
- Tension problems on the belt should be fixed if you want to ensure optimal performance.
- The bleed rate works best it is adjusted accordingly to complement the local quality of water and evaporation regulations. What is more, adjusting bleed rates also help with the accumulation of solid particles.
- Lubricate the shaft bearings of the fans once every three months at the least. This maintains the proper operation of the fans. To maximize the potential, try installing automatic greasers at the bearings. It is rather easy and it eliminates the need for excessive monthly maintenance.
- Oil levels and oil quality, as well as the alignment of the gear drive shafts, must be checked from time to time. Check with the manufacturer and their recommendation on the correct way of doing so.