Glass bottle manufacturing has been around for centuries, and while the basic process of melting glass and shaping it into a bottle has remained the same, new technologies and innovations are transforming the industry. With a growing focus on sustainability and environmental concerns, glass bottle manufacturers are exploring new ways to reduce waste, increase efficiency, and produce bottles that are both eco-friendly and visually appealing.
Glass bottle manufacturers are working towards developing new technologies and innovations to create more sustainable and eco-friendly products. They are exploring various avenues to reduce their carbon footprint and make the glass bottle production process more efficient. These efforts are not only beneficial for the environment but also for manufacturers’ bottom lines.
In this article, we will delve into the latest developments in glass bottle manufacturing, from cutting-edge manufacturing processes to innovative design and material advancements. We will also discuss the potential impact of these advancements on the industry and what future manufacturing might look like.
Lightweight Glass Bottles
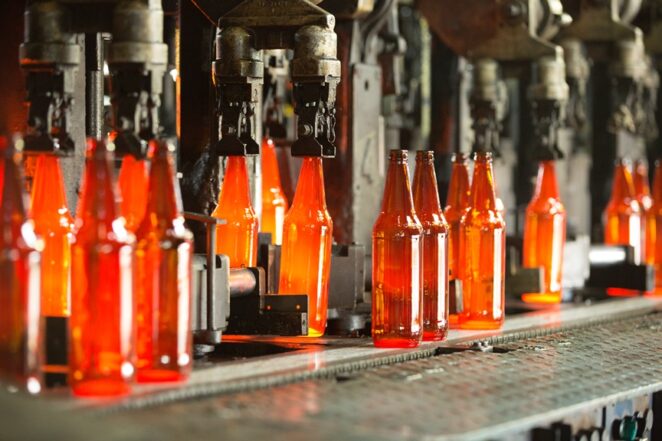
The main disadvantage compared to other materials like plastic or aluminum is their weight. This makes them more expensive to transport and can increase the carbon footprint of a product. To address this issue, glass manufacturers are developing new formulas and techniques to create thinner and lighter glass bottles that retain their strength and durability. This would not only reduce transportation costs but also lower the environmental impact.
Electric Melting Furnaces
Glass production is an energy-intensive process that requires high temperatures to melt the raw materials. Traditional gas-fired furnaces are notorious for their emissions and inefficiencies. However, the use of electric melting furnaces is gaining momentum in the glass industry. These furnaces use electricity to heat the glass, reducing the number of carbon emissions and improving the overall energy efficiency of the production process.
Automation and Robotics
The glass manufacturing process involves many repetitive tasks that are labor-intensive and require high precision. This is where automation and robotics come in. By automating certain parts of the production process, manufacturers can improve efficiency, reduce waste, and increase product consistency. For example, robots can be used to handle and inspect glass bottles, reducing the risk of defects and improving quality control.
Use of digitalization to optimize production processes and reduce waste
The use of digitalization in glass bottle manufacturing can greatly improve production processes and reduce waste. Digitalization involves the use of digital technologies to streamline and optimize manufacturing processes, resulting in greater efficiency and reduced waste.
One way that digitalization is being used in reflector bottle manufacturing is through the implementation of sensors and data analytics. Sensors can be installed throughout the production process to collect data on factors such as temperature, pressure, and humidity. This data can then be analyzed using advanced data analytics tools to identify areas where production processes can be optimized, reducing waste and increasing efficiency.
Digitalization can also be used to improve supply chain management, enabling manufacturers to better track and manage raw materials and finished products. This can help to reduce waste and improve overall efficiency by ensuring that materials are used effectively and that products are delivered to customers on time.
Recycled Glass
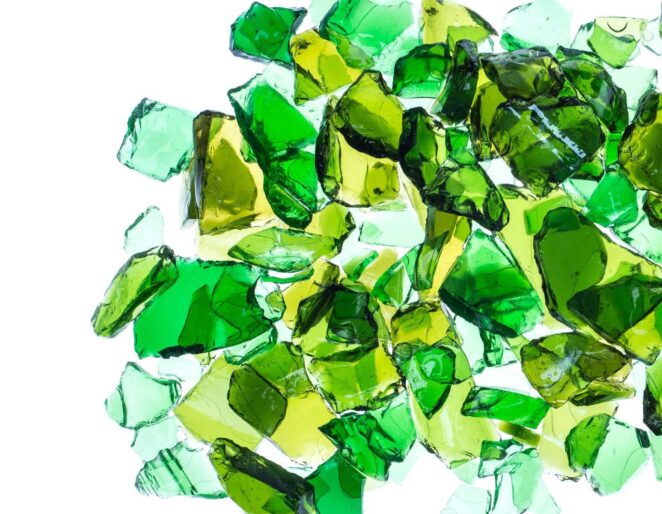
One of the most significant trends in the packaging industry is the move towards a circular economy, where waste is minimized, and resources are reused. Glass is an ideal material for recycling since it can be melted down and used to make new bottles without losing quality. Glass manufacturers are investing in recycling infrastructure and technology to increase the use in their production processes. This not only reduces the environmental impact but also creates a more sustainable supply chain.
Smart Glass
In the age of the Internet of Things (IoT), even glass bottles can become smart. By embedding sensors and chips in the glass, manufacturers can track the product’s journey from production to consumption. This information can be used to improve logistics, inventory management, and consumer engagement. For example, a smart glass bottle can send reminders to consumers to refill or recycle the bottle or provide personalized recommendations based on their preferences.
Future Outlook and Potential Impact
The potential impact of new technologies and innovations in glass bottle manufacturing is significant. Advancements in automation and digitalization can increase efficiency and reduce waste, while the use of innovative materials and designs can appeal to consumers and meet sustainability goals. Energy efficiency and emissions reduction initiatives can also play a crucial role in reducing the industry’s environmental impact.
Moving forward, the glass bottle manufacturing industry must balance the need for sustainability with consumer preferences and market demands. As more consumers prioritize eco-friendliness and demand sustainable packaging options, glass bottle manufacturers must continue to innovate to meet these expectations. There may also be opportunities for collaboration between glass bottle manufacturers and other industries, such as the beverage industry, to further reduce the environmental impact of packaging.
Opportunities and challenges for the industry moving forward
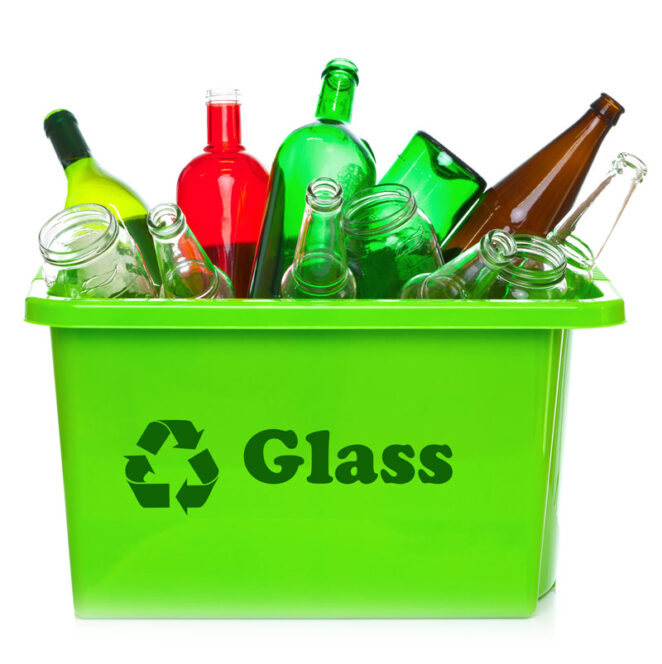
The glass bottle manufacturing industry face both opportunities and challenges as it moves forward. Opportunities include the potential for increased sustainability through the use of new materials and technologies, and the ability to meet changing consumer preferences for eco-friendly packaging. Collaboration with other industries and stakeholders can also create new opportunities for growth and innovation.
However, the industry also faces challenges, such as the need to balance sustainability goals with production costs, and the need to adapt to changing market demands. Other challenges include maintaining quality standards while implementing new technologies, and managing the transition to more sustainable production processes.
Conclusion
In conclusion, future manufacturing looks bright with new technologies and innovations on the horizon. From advancements in automation and digitalization to improvements in material science, the industry is poised for significant change. As consumers continue to demand more sustainable and eco-friendly packaging options, glass bottle manufacturers are investing in new technologies to reduce their environmental impact and improve efficiency.
These innovations will not only benefit the industry but also contribute to a more sustainable future for our planet. It will be interesting to see how these new developments will shape future manufacturing in the years to come.